
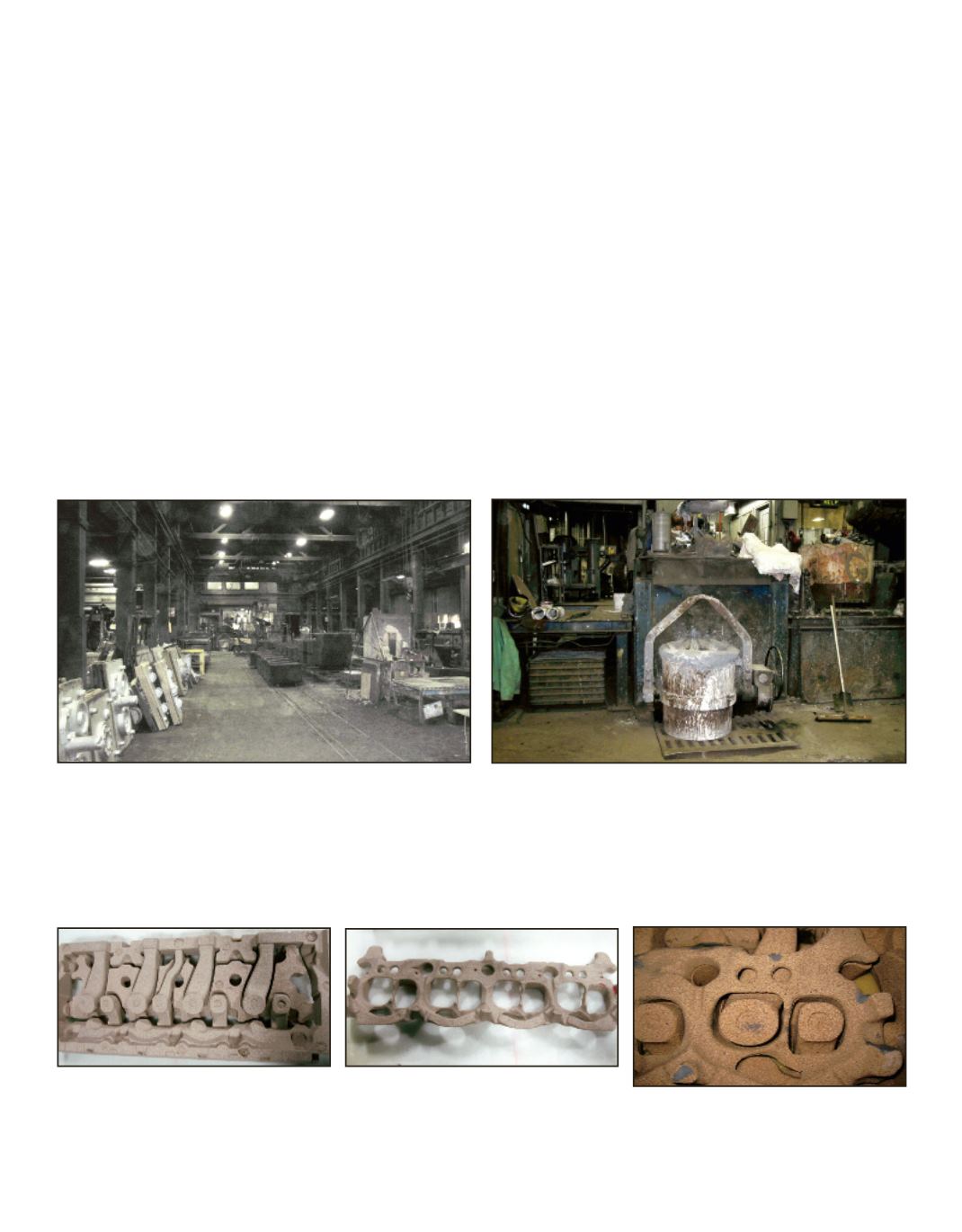
chined in-house by TOE Performance.
This satisfied the demand between the
late 1980s and early 1990s. A set of
machined bare GT40 heads, at that
point, cost about $3,000. In addition to
that, a first-class, professional porting
job cost around $6,000.
The way things like this tradition-
ally play out, an inability to find desir-
able parts, such as GT40 heads,
creates a demand. When that demand
reaches a level where the cost of repro-
ducing them can be recouped, someone
will undertake a production run. In
time, the new supply is reduced to the
point where it no longer exists. This
was the case in 2000. Rather than im-
mediately engage in another produc-
tion run, take on the up-front costs
and then watch sales continue to
plateau, the usual tendency is to wait
for a demand to build.
Rather than wait, however, TOE
Performance sold the C6FE GT40
head tooling to Robert Pond/Robert
Pond Motorsports in Riverside, Cali-
fornia in 2010. After two attempts to
make a small production run of about
20 heads, of which only a few were ac-
ceptable,
Pond entered into a partnership
with Curt Vogt/Cobra Automotive in
Wallingford, Connecticut in 2016. As
an engine builder and someone who
operates a large vintage race car
preparation shop, Vogt, like other en-
gine builders around the country,
could not find useable GT40 heads.
There was an especially serious need
by European racers whose engines
had to meet very stringent, date-spe-
cific mechanical requirements and
were not allowed to use aftermarket
heads. There was also an ongoing de-
mand for these heads by vintage rac-
ers intent on competing in the
Monterey vintage race.
Vogt had extensive experience in
pattern-making, casting and working
with foundries, so he was the perfect
person to front-run the project. He lo-
cated a small, family-run foundry,
Fairmont, in Woonsocket, Rhode Is-
land. Cast-iron heads are difficult to
produce and many larger foundries do
lot want to bother with small produc-
tion runs. Fairmount is run by two
brothers who have a personal interest
in high performance cars. They both
wanted to see this project completed.
Once the castings are finished,
they are shipped to a machine shop in
Ohio where they are completed. They
are sold bare, for between $3,000 and
$3,500 a pair. Five-access CNC ma-
chining porting will be extra. The first
production run was 25 sets. Cobra Au-
tomotive is the sole distributor.
jgaruti@cobraautomotive.com
The SHELBY AMERICAN
Summer 2017 66
The foundry production floor where the molds are poured.
Fifty years ago there were cast iron foundries in every
large city in this country. Today, due to strict Department
of Environmental Protection regulations, most of the
smaller and medium-sized cast iron foundries have been
put out of business. Larger foundries remain but they rely
on large production runs. Most foundry business is now in
Mexico or China.
The crucible is where the cast iron is heated to 2650°. The
molten metal is ladled or poured into the mold where it
fills all of the cavities and hollow spaces. Air, excess sand
and impurities are forced out of the mold. After the casting
has cooled the mold is disassembled, revealing the fin-
ished casting. Before it can be machined unnecessary
pieces are broken off and flashings ground off.
Cores within the mold create cavi-
ties – water jackets, intake and ex-
haust ports, combustion chambers and
oil drain holes.
Detail of the core around the intake
and exhaust areas.
The water jacket core creates the cav-
ities around the combustion chambers
and valve ports.